Plant for manufacture of a basalt superthin fiber (BSTF)
Plant consists of small-sized melting furnaces with automatic loaders of a basalt crumb.
Through heat resisting (or from platinum-rhodium alloy) feeders by means of extending devices
are formed initial fibers in diameter up to 300 microns. Fibers move in chambers of blowing
where they are blew by a high-speed stream of combustion of a gas-air mix in staple superthin
fibers in diameter 1-3 microns. Length of fibers of 50-70 mm. Superthin fibers get in the
chamber of fiber sedimentation and are precipitated on a drum of the conveyor.
Formation of a commodity canvas is made on the takeup unit device.
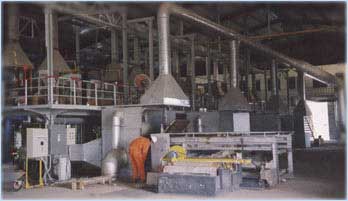 |
General view of manufacture |
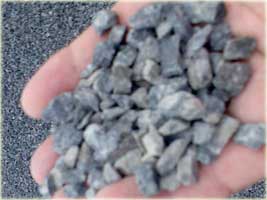 | 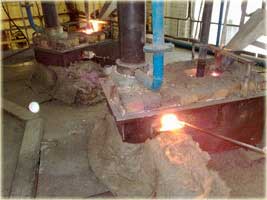 |
Raw material - a basalt crumb | Melting furnace |
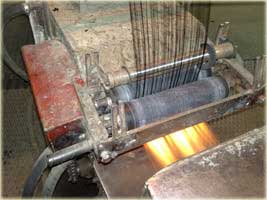 |
Reception and having inflated primary fibres |
At application automatic pickup, the canvas moves directly on technological lines for its further processing.
Now we can offer installations BSTF with following characteristics.
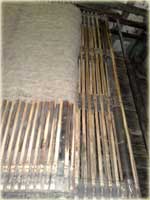 | 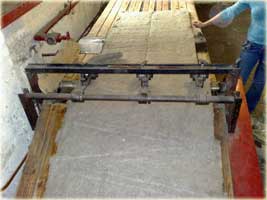 |
Automatic destacker a canvas | Processing of a canvas |
THE BASIC CHARACTERISTICS OF PLANTS
Table 26
The name of parameters |
Mark of plants * |
BSTF-H-01 |
BSTF-PR-01 |
BSTF-H-02 |
BSTF-PR-02 |
Productivity on a fibre, t/year | 120,0 | 180,0 | 200,0 | 320,0 |
The charge of natural gas **, m3/kg | 3,0 | 2,0 | 2,2 | 1,5 |
The charge of the electric power, kW/kg | 3,3 | 3,0 | 3,1 | 2,6 |
Overall dimensions, m Width Length Height | 6,0 6,0 7,0 | 6,0 6,0 7,0 | 6,0 8,0 7,0 | 6,0 8,0 7,0 |
The attendants, person/shift Operators | 2 | 2 | 3 | 3 |
* H- on heat resisting feeders
** use diesel fuel or black oil is possible.
PR - on platinum-rhodium feeders
Term of guarantee service of heat resisting feeders depending on structure of a heat
resisting alloy - 20 - 80 day, platinum-rhodium - 6 months.
The structure of plant includes following units:
the loader-batcher, the furnace melting, a recuperator, the unit of formation the
extending mechanism, unit of blowing, diffuser, the chamber faber precipitation,
units and details of system of turnaround water-cooling, units and details of system
gas-air supply, an electric equipment (control panels, cable distributing), transformers
of type ÒÂÊ-75, fans of a high pressure of type FHP (are applied to group of 3 plants),
smoke sucker, a platform of service, the chamber of clearing of departing gases.
COST:
Cost of BSTF depends on completeness and a degree of automation. Recommended capacity
of profitable manufacture, BSTF, allowing in the shortest terms to pay back initial
expenses makes 500-600 t/year.
For an example manufacture by productivity 1000 t/year.
Manufacture is based on technology of reception of a basalt superthin fibre with
application of unicomponent mineral raw material - basalt.
Manufacture BCTF and products on its basis is offered to be organized with use of
modern technological decisions and on new element base and to have the automated control system.
Proposed assortment of made production from BSTF:
- canvases from basalt superthin fibres;
- material termal insulation and sewing-knitting;
- basalt termal insulation cord;
- telmal insulation cardboard and plates on a basis polyvinylacetate emulsion;
- termal insulation cardboard and plates on the basis of clay binding.
The assortment and volume of production on basis BSTF is specified and defined at joint discussion with the customer.
Manufacture is planned to place in the one-storeyed building having dimensions:
- width - 36ì;
- length – 72 ì;
- high – 8ì.
Dimensions of a building are specified during designing in view of specifications of the Customer.
Manufacture BSTF by capacity includes 1000 t/year of the seven modules - installations
mounted on a technological metal platform with mark ± 2.500.
Productivity of the module, not less - 150 t/year
The technological platform is intended for accommodation 7 installations BSTF:
- melting furnaces – 14 pcs.
- systems of loading and submission of raw material;
- systems of heating of furnaces;
- electric equipment with a board control equipment;
- systems of water supply junction of the melting furnace.
Other equipment is placed on mark. ± 0.000.
1. For manufacture BSTF in shop auxiliary premises and sites are provided:
- site of storage, preparation and submission of raw material;
- room of compressor station;
- system of turnaround water supply;
- electropanelboard;
- ventilation room;
- system of reserve electrosupply;
- site airsupply;
- intermediate warehouse;
- packing branch;
- warehouse of finished goods;
- mechanical-repair site;
- electromechanical site;
- room of shop laboratory and Quality Department;
- room of engineering services;
- household rooms for working;
- room of controller's office (for production management and the economic analysis of job of the enterprise);
2. Structure of the equipment technological modules - installations BSTF -150:
- Platform technological (1 section) - 1
- Furnace melting – 2
- The loader – 2
- Recuperator – 2
- unit heating a feeder – 2
- feeder – 4
- unit of formation of a primary string – 2
- unit of bulge – 2
- diffusion cell – 2
- the chamber of sedimentation – 1
- system of heating of the furnace – 1
- units of water-cooling - the complete set
- installation of removal and filtration of departing gases – 1
- the ventilating unit – 1
- board of the operator – 1
- board founder – 1.
3. Technological process of manufacture BSTF
Installation will consist of small-sized melting furnaces with automatic loaders of a basalt crumb.
Through heat resisting (or from platinum-rhodium alloy) draw plate feeders with the help of extending devices are formed primary fibres in diameter up to 300 microns.
Fibres move in chambers blowing where they are inflated by a high-speed stream of combustion of an air-gas mix in staple superthin fibres in diameter 1-3 microns. Length of fibres of 50-70 mm.
Superthin fibres get in the chamber fiberdeposition and are besieged on a drum of the conveyor. Formation of a commodity canvas is made on bobbin machine.
At application automatic pickup, the canvas moves directly on technological lines for its further processing.
4. Requirement for power resources of the module BSTF-150
the Equipment of the module |
the Kind of power resources |
Units of measurements |
Rating values |
the Point of a supply |
the Furnace melting (2 pcs.) |
Gas natural |
mm 3 /hour |
12õ2 =24 |
the Internal gas main to torches of the furnace |
the Loader (2 pcs.) |
the Electric power |
kw |
0,5 |
the Control panel |
Unit heating a feeder (2 pcs.) |
Water turnaround pressure, not less, than 0,3 mPa
The electric power |
m3 / hour
kw
|
1,5
30
|
The union of cooling
Boards of the operator
|
Unit of formation of a primary string (2 pcs.) |
Water turnaround |
|
1,5 |
the Union of cooling |
Unit bulge |
Water turnaround
Gas natural
Air
|
M 3 /hour
Mm 3 /hour
M 3 /mines (m 3 /hour)
|
6
20õ2=40
8
|
The union of cooling
Gas main to the chamber bulge
From the air compressor to the chamber bulge
|
Installations of removal and a filtration of departing gases |
The electric power
Water turnaround
|
Kw
M3 / hour
|
15,0
0,3
|
To a board of the operator
The union to the chamber of clearing
|
5. Charges of power resources on the process equipment of manufacture BSTF capacity 1000.
(annual fund working hours 330õ24 = 7910 hours)
¹ ï/ï
|
the Name of a parameter |
Units of measurements |
Size * |
1 |
Gas natural with caloricity 33,5 mjoule/m 2 (8000 kcal / m 3 ) |
m 3 /hour
M3/year
|
450
3,6õ106
|
2 |
the Electric power of 3 phases; 380V±10 %; 50Hz
|
kilowatt-hour
One thousand kilowatt-year
|
350
2,772
|
3 |
Water technical turnaround pressure, not less than 0,3 MPa
|
m3/hour |
65 |
4 |
Air compressor pressure, 0,8-1,0 kg / sm 2 (0,08-0,1) MPa
|
m3/min
m3/hour
|
70
4200
|
6. Requirement of the attendants for manufacture BSTF
the Industrial personnel:
The operator of submission of raw material - 4
Glass founder - 8
The operator of unit fibrelization - 28
The leaser of production - 8
Total: 48 person.
Support personnel:
The on duty mechanic - 4
The on duty electrician - 4
The on duty mechanic of control equipment - 4
The on duty sanitary technician - 4
The controller of Quality Department - 2
Total: 18 person
|
|